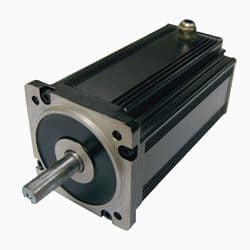
Permanent Magnet DC Generator
Permanent Magnet DC Generator as a Wind Power Generator
We know from the previous wind turbine tutorial, that an electrical generator is a rotational machine that converts the mechanical energy produced by the rotor blades (the prime mover) into electrical energy or usable power. This energy conversion is based on Faraday’s laws of electromagnetic induction, that dynamically induces an e.m.f. (electro-motive force) into the generators coils as it rotates. There are many different configurations for an electrical generator, but one such electrical generator which we can use in a wind power system is the Permanent Magnet DC Generator or PMDC Generator.
Permanent magnet direct current (DC) machines can be used as either conventional electric motors or as DC wind turbine generators, since constructionally there is no basic difference between the two. In fact, the same PMDC machine may be driven electrically as a motor to move a mechanical load, or it may be driven mechanically as a simple generator to generate an output voltage. This then makes the permanent magnet DC generator (PMDC generator) ideal for use as a simple wind turbine generator.
If we connect a DC machine to a direct current supply, the armature will rotate at a fixed speed determined by the connected supply voltage and its magnetic field strength thereby acting as a “motor” producing torque. If however, we mechanically rotate the armature at a speed higher than its designed motor speed by using rotor blades, then we can effectively convert this DC motor into a DC generator producing a generated emf output that is proportional to its speed of rotation and magnetic field strength.
Generally with conventional DC machines, the field winding is on the stator and the armature winding is on the rotor. This means that they have output coils that rotate with a stationary magnetic field that produces the required magnetic flux. Electrical power is taken directly from the armature via carbon brushes with the magnetic field, which controls the power, being supplied by either permanent magnets or an electromagnet.
The rotating armature coils pass through this stationary, or static magnetic field which in turn generates an electrical current in the coils. In a permanent magnet DC generator, the armature rotates so the full generated current must pass through a commutator or slip-rings and carbon brushes arrangement providing electrical power at its output terminals as shown.
Typical DC Generator Construction
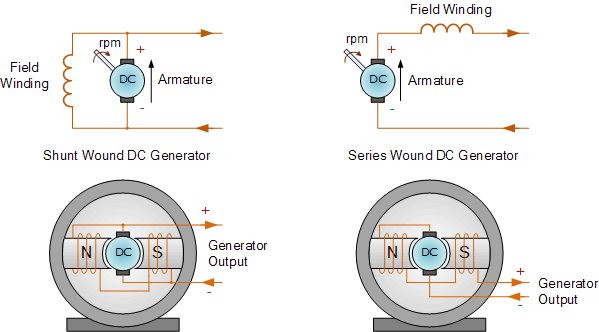
A simple DC generator may be constructed in a variety of ways depending upon the relationship and interconnection of each of the magnetic field coils with respect to the armature. The two basic connections for a self-excited DC machine are the “Shunt Wound DC Generator”, in which the main field winding is connected in parallel with the armature. The “Series Wound DC Generator”, has the current carrying field winding connected in series with the armature. Each type of DC generator construction has certain advantages and disadvantages.
Shunt Wound DC Generator – In these generators, the field (excitation) current, and hence magnetic field, increases with operating speed as it is dependent upon the output voltage. The armature voltage and electrical torque also increase with speed. The shunt-wound generator, operating at a constant speed under varying load conditions, has a much more stable voltage output than does the series-wound generator. However, as the load current increases the internal power loss across the armature causes the output voltage to decrease proportionally.
As a result, the current through the field decreases, reducing the magnetic field and causing voltage to decrease even more and if load current is much higher than the design of the generator, the reduction in output voltage becomes so severe resulting in large internal armature losses and overheating of the generator. As a result, shunt wound DC generators are not normally used for large constant electrical loads.
Series Wound DC Generator – The field (excitation) current in a series wound generator is the same as the current the generator delivers to the load as they are both in series. If the connected load is small and only draws a small amount of current, the excitation current is also small. Therefore, the magnetic field of the series field winding is too weak and the generated voltage is also low.
Likewise, if the connected load draws a large current, the excitation current is also high. Therefore, the magnetic field of the series field winding is very strong, and the generated voltage is high. One main disadvantage of a series wound DC generator is that it has poor voltage regulation, and as a result, series wound DC generators are not normally used for fluctuating loads.
Both Shunt Wound and Series Wound self-excited DC generators have the disadvantage in that changes in load current causes severe changes in generator output voltage due to armature reaction and as a result, these types of DC generators are seldom used as wind turbine generators.
However, a “compound” connected DC generator has a combination of both shunt and series windings incorporated into a single generator and which can be so connected as to produce either a “short-shunt compound DC generator” or a “long-shunt compound DC generator”. This type of self-excited DC generator design allows for the advantages of each type to be included into one single DC machine.
Another way to overcome the disadvantages of a self-excited DC generator is to allow the field windings to be externally connected. This then produces another type of DC generator called a Separately Excited DC Generator.
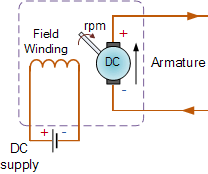
As the name suggests, a separately excited DC generator is supplied by an independent external DC power source for the field winding. This allows the excitation current to produce a constant magnetic field flux regardless of the load conditions on the armature. With no electrical load connected to the generator, no current flows and only the generators rated voltage appears at the output terminals.
If an electrical load is connected across the output, current will flow and the generator will begin to deliver electric power to the load.
A separately excited DC generator has many applications and can be used in high wind turbine generator applications. However, DC generators for wind turbine applications have the disadvantage that a separate direct current power source is needed to excite the shunt field. However, we can overcome this disadvantage by replacing the field winding with permanent magnets, creating a Permanent Magnet DC Generator or PMDC Generator.
Permanent Magnet DC Generator
The Permanent Magnet DC Generator can be considered as a separately excited DC brushed motor with a constant magnetic flux. In fact, nearly all permanent magnet direct current ( PMDC ) brushed motors can be used as a permanent magnet PMDC generator, but as they are not really designed to be generators, they do not make good wind turbine generators because when working as a simple DC generator, the rotating field acts like a brake slowing down the rotor.
These DC machines consist of a stator having rare earth permanent magnets such as Neodymium or Samarium Cobalt to produce a very strong stator field flux instead of wound coils and a commutator connected through brushes to a wound armature as before.
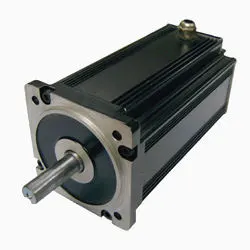
When used as permanent magnet DC generators, PMDC motors generally have to be driven a lot faster than their rated motor speed to produce anything near to their rated motor voltage so high voltage, low rpm DC machines make better DC generators.
The main advantage over other types of DC generator is that the permanent magnet DC generator responds to changes in wind speed very quickly because their strong stator field is always there and constant.
Permanent magnet DC generators are generally lighter than wound stator machines for a given usable power rating and have better efficiencies because there are no field windings and field coil losses.
Also, as the stator is provided with a permanent magnet pole system, it is resistant to the effects of possible dirt ingress. However, if not fully sealed, the permanent magnets will attract ferromagnetic dust and metallic swarf (also called turnings or filings) which may cause internal damage.
The permanent magnet DC generator is a good choice for small scale wind turbine systems as they are reliable, can operate at low rotational speeds and provide good efficiency especially in light wind conditions as their cut-in point is fairly low.
There are many “off-the-shelf” permanent magnet DC generators available with a wide range of power outputs from a few watts to many thousands of watts. The DC voltage generated by a permanent magnet DC machine is governed by the following three factors:
- The magnetic field developed by the stator. This depends upon the physical size of the generator and the strength and type of the permanent magnets used.
- The number of turns or loops of wire on the armature. This value is fixed by the physical size of the generator and armature and by the size of wire conductor. The more turns used the higher the output voltage. Likewise, the larger the wire diameter or cross sectional area the higher the current.
- The rotational speed of the armature which is governed by the speed of the wind turbine rotor blades relative to the high wind velocity. For PMDC generators and motors, output voltage is proportional to speed and is generally linear.
The most common type of DC generators for wind turbines and small scale wind turbine systems used to charge batteries is the permanent magnet DC generator, also know as the Dynamo. Dynamos are a good choice for newcomers to wind power as they are large, heavy and generally have very good bearings, so you can mount fairly hefty rotor blades directly onto their pulley shaft.
Old style diesel truck or bus dynamos are a better choice for wind turbines as they are designed to generate the required voltage and current at slower speeds with the emphasis on efficiency rather than on maximum power. Also, most bus and truck dynamos can generate power up to 500 watts at 24 volts which is more than enough to charge batteries and power lights for a small scale low voltage system.
Other types of PMDC motors that are suitable for wind power DC generators include traction motors used in golf carts, fork lifts and electric cars. Usually these motors are 24, 36 or 48 volt types with high efficiencies and power ratings.
One of the main disadvantages of a permanent magnet DC generator, is that these machines have commutating brushes that carry the full output current of the generator so DC machines used as dynamos and generators require regular maintenance as the carbon brushes used to extract the generated current quickly wear out and produce a lot of electrically conductive carbon dust inside the machine. Therefore, AC alternators are sometimes used.
Car alternators are another very popular choice as a simple DC generator for use as a wind turbine generator, especially among newcomers and DIY enthusiasts as low voltage DC can also be generated by alternators. Most automotive alternators contain AC-to-DC rectifiers that supply DC voltage and current. In an alternator, the magnetic field rotates and the variable 3-phase AC which is generated by the stationary stator coils is converted into 12 volts DC by an internal rectifier circuit. Automotive alternators have the distinct advantage that they are specifically designed to charge 12 or 24 volt batteries.
Enclosed PMDC generators are preferred in wind turbine generator systems to protect them from the elements, but standard car alternators are usually open and cooled by ambient air ventilated through the generator so some additional form of weather protection is require. They also come in a variety of sizes and power ratings designed for small cars to large trucks and while they may be cheap and and readily available, they are not very efficient compared to the larger permanent magnet DC generator.
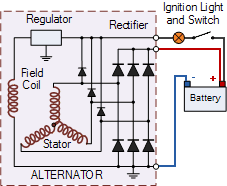
The key to simplicity and increased efficiency comes from building a direct drive wind turbine with the turbines blades mounted directly onto the generators main pulley shaft. As soon as you introduce gears, belts, pulleys, or any other ways to increase or decrease their speed, you introduce energy losses, additional costs and complexity.
Although a good five or seven foot (1.5 to 2 metres) diameter three-bladed rotor will reach speeds in excess of 1,000 rpm, this is still too slow to be a good match for most common car alternators that rotate at speeds of between 2,000 and 10,000 rpm as they are attached to the cars engine. Then some sort of gearbox or pulley system would be required to increase the speed at which the alternator spins, and to increase the output of the alternator.
Also, automotive alternators require an additional external power supply to provide a small biasing current (usually through the dashboard indicator lamp) to their field coils to start the excitation and therefore the generation process before the alternator reaches its cut-in speed.
This external field current could be supplied by the attached battery bank but the problem with this is that the batteries would continually supply current to the field winding, possibly draining the batteries even when the turbine blades are stationary during periods of zero or little wind. Another problem with modern automotive alternators is that they are built for cheapness and light weight so usually only have small 5/8 inch or 17 mm diameter rotor shafts to mount a pulley on which may be a little on the small side to take the weight and stresses of the rotating blades.
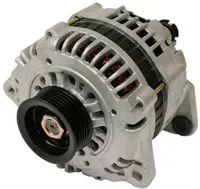
One of the hardest parts of designing a small scale low voltage wind turbine for electricity production is to finding a suitable DC generator.
The Permanent Magnet DC Generators is a low speed generator that are pretty reliable and efficient in light winds for use in “off-grid” stand alone systems to charge batteries, or to power low voltage lighting and appliances. They generally have linear power curves with low cut-in speeds of around 10 mph. Unfortunately, old style permanent magnetic DC generators which are larger, heavier and more robust are becoming more difficult to find.
As well as Permanent Magnet DC Generators, the automotive car alternator is also another popular choice among many do-it-yourself people for use as a low voltage DC generators for wind turbines. However, being a an automotive alternator bolted to the side or a combustion engine, they require high rpm speeds to generate power and are not always very efficient. Car alternators also require an external power supply voltage to power the electromagnets that create the internal magnetic field.
Car alternators limit their own current using a built-in regulator circuit which also stops the alternator from overcharging the connected batteries. However, an automotive alternator should never be connected to the battery bank in reverse or run the alternator at high speeds without the battery connected, as the output voltage will rise to high levels (much more than 12 volts) and destroy the internal rectifier.
Low voltage stand alone wind power systems are great for wind charging batteries etc, but if we want to power larger mains connected appliances or have a system that is “grid-tied” we need to either use some form of inverter to change the low voltage DC generated by the permanent magnet DC generator into a higher voltage (120 or 240 volts) AC supply, or install another different type of wind turbine generator.
In the next tutorial about Wind Energy, we will look at the operation and design of a different type of electrical machine called a Synchronous Generator. The synchronous generator is very different from a permanent magnet DC generator because it can be used for generating three-phase grid connected AC or alternating current electricity.
Dear Customer,
Glad to meet you here.
Could I share more information about our products with you to make you get high performance permanenet magnet DC generators?
Looking forward to yourfeedback.
Sincerely yours,
Ashley
Sir, with good hope I have 2kw grid tied rooftop pv solar lant on my house terrace and now i am interested to install more 1kw small wind turbine with grid tied hybridly with existing grid tied solar. please suggest what type PMDC generator can install and How it is connect with solar plant. series or parallel with solar plant OR can i install with same inverter OR separate inverter is required ,
What type of generator would you recommend to be used to help produce power to a small home or maybe camper? If one could run a small home like a portable generator you buy at the store would, which one could handle fluctuation and demand of power when power is turned on (ex. lights, fans, or a refrigerator)?
Clearly, the type, wattage and size of a portable generator would depend on what it has to supply, 120V, 240V, 3-phase and the number of kilo-watts, etc. Small horsepower generators are cheaper and run on gasoline. Larger horsepower generators can handle larger AC loads and run on gasoline, diesel fuel, or propane.
I have a 12V PMDC blower motor where the field stator is PM and wound armature with commutator not + and – ring terminals. I know the RPM should be high but I turned it with my 18V chargeable drill and connected to a 12V indicator bulb that will take only a little current but it did not light up.
What is wrong? as it is filament bulb AC or DC doesnt matter and it should light up. is the generated power consumed af hysterical reverse power? How to avoid and make it work?
Also I can get a 40A alternator but do I have to modify by installing magnets on to the armature?
PMDC motors use permanent magnets to produce the required magnetic field. The armature is made up of several wire loops and the commutator has several segments. Each wire loop consists of several turns of wire instead of a single turn. When the armature is rotated within the stator’s permanent magnet field, the magnetic flux that passes through the armatures loops varies and a voltage is induced across the loop terminals. This generated voltage is proportional to the rotation speed of the armature. This is because the higher the rotation speed of the armature, the higher the rate of change of the magnetic flux and thus, the higher the generated voltage. Also, the polarity of this voltage depends on the direction of rotation.
For a PMDC motor operating as a generator, it will be easy to rotate the motor shaft with its terminals open-circuited, but much harder when the terminals are loaded or short-circuited. This is because a force (torque) opposing armature rotation is produced internally with this torque being in opposite direction to the rotation. Also, the higher the current supplied to the load, the stronger the torque opposing rotation. Then your lamp will be seen by the generator as a low value resistive load, producing less output voltage. Start by rotating the motor at a higher rotational speed and measure the terminal voltage unload using a digital multimeter/voltmeter.
what would be the best low speed permanent magnet brushless self exiting generator to use to power 15 x5 watt led lights i want to use it on a conveyor belt the belt moves at 2.4 meter per second my supply circuit will be 12 volt DC to a invertor
Sir,
I am trying to develope one wind generator ,to charge battery of EV vehicle. Which one is batter choice- altornator , PMDC GENERATOR OR DC MOTOR. please guide
Brushless DC permanent-magnet generators are a better choice for micro-wind turbine applications as their lack of brushes improves efficiency, better reliability, and longer life with less maintenance
Hello ,
A while ago I came across a permanent magnet motor Model number MDD112C-L-020-N2L-130GA0. Can this be used to generate power . Please if it was possible i would post some photos of the motor and its specs.
Servo Motors can be used as generators to a point, but they are AC machines so rectification at the required current is required. Also you would need to match the servo with the load for maximum power transfer and probably have to run it at a high rpm speed as its a two, or four-pole synchronous machine whose frequency is synchronised with its mechanical rotational speed.
If I use a 12 V DC motor and connect it to charge a battery, the battery will turn the motor. How do I prevent this?
Use a charge controller, rectifier or diode
Hi.
Pls look at the idea.
startup.ua/en/projects/411997.html
She may like and be interested!
For the evaluation and like, a special thanks:)
Thanks.
sir i want to make fuel less generator with permanent magnet alternator and slip ring induction motor, would it be possible to get electricity from this by connecting them through pulleys and for starting them we can use batteries or some external power
yes you can do it but it will not be that efficient . but for the sake of the argument it works
is any constraints for WIND SPEED FORECASTING STUDIES
No, just measure and understand the wind speed and direction for your location and use the data collected to produce a wind speed distribution graph.
If I use pmdc generator for wind turbine out put voltage is constant or not Out put voltage is dependent on speed or not
I have 3 15 HP Permanent Magnet, DC Motors. They are rated at 180 Volts. They are in good working condition. Are they valuable as DC Generators to anyone???? I don’t think I will use them & do not want to scrap them
I would really like to have that for an experiment
I beg to differ on the DC output….all coils going through a field coil put out a sine/cosine wave which in turn causes voltage…magnetism…decay of magnetism in both sides of the + or – sides of the magnets 180 degrees out from each other…
The build of the wave of power and the decay of the wave of power and magnetism collapse creates a bell curve of power that goes through the zero point of power before making the opposite side of the zero line.
Basically all generation is AC and then through diodes….one way switches of either plus or minus for the coils being charged with a North or a South pole do we rectify the power to a DC current….called a bridge rectifier…
Hope that helps more than hurts but this is the basic theory that should be understood!
The flaw in your argument is that you forgot to mention the commutator and brushes, or even lap and wave winding configurations. This also is the basic theory of DC generators that should be understood!
Generators are power generation appliances that supply electrical power during a power outage and prevent discontinuity of power activities or disruption of business operations. Generators are available in different electrical and physical specifications for use in different applications.
It is a very informative knowledge given in this page, but just I want to clear my mind from some question. Some of the guy I know told me that any PMDC motor/generator is giving an output of AC voltage. I’m puzzled as through my common knowledge, it suppose to be a dc voltage output. Please explain. By the way, is there any possible to make (DIY) a pure sine inverter (DC to AC) circuit? Thank you.
As its name implies, a Permanent Magnet DC (PMDC) generator is a continuous current machine. A DC machine, called a Generator, has a commutator generating a continuous DC supply. Whereas an AC machine, called an Alternator, has slip-rings generating a sinusoidal supply.
There are numerous schematic diagrams available on the internet regarding DIY circuits for pure sinewave inverters.
Thanks a lot. That is a great yet informative explanaition. Btw, I am sorry for this late reply.
You really help me, especially my companion who said that he wanted to build a green energy machine works like a hydro-dam.
the information is very rich and appropriate. what is the price for the DC Generator
There is any mechanical rotation torque losses occur
Yes, as with any rotating machine there will always be mechanical losses due to windage losses, bearing friction losses and the connected load creating a drag torque.
The brushed series DC motor is the most affordable and readily available current production motor for road-going conversions available today. Brushless DC motors require expensive controllers. Permanent magnet motors are very efficient, but only in a very narrow rpm band, and quickly lose their efficiency in the varying speeds of normal driving. Shunt and compound motors are more expensive to build and have poorer acceleration than series motors. For these reasons, the brushed series DC motor is the motor of choice for DC systems.